So just a quick recap...
If you are glassing surfboards and you need a nice crystal clear shiny finish, you can put what they call a "sand coat" over the glass after you do the layup. This is just another coat of resin that will fill the weave of the cloth so that you can sand it smooth without having to sand into the fibers of the cloth so much. After sanding the whole thing smooth, I believe the surfboard guys then do one more coat of resin which is the one that will be polished to a shiny finish. (Our buddy Travis can probaby tell us that. :mrgreen: )
For what we are doing here, all we care about is that the surface is smooth. So instead of using resin, which would take another whole day to harden, I just filled the weave with bondo. A few coats of high build primer over that and we will be good to go.
One other thing I didn't mention is that for something like this where I want the surface to be fairly flat, I use sanding blocks as opposed to hand sanding. Here are a few of the ones I've made for different things - different sizes and grits for different purposes. (The chunk o' pipe works great for doing wing fillets on airplanes. :mrgreen: ) I am even using a block to wetsand the primer to keep everything flat. A final note about sanding blocks is that the sand paper will last much longer when glued to a block of wood. I guess because it is not flexing, so it doesn't break apart like it would if you were hand sanding. I've had some of these for years and they still work great!
If you are glassing surfboards and you need a nice crystal clear shiny finish, you can put what they call a "sand coat" over the glass after you do the layup. This is just another coat of resin that will fill the weave of the cloth so that you can sand it smooth without having to sand into the fibers of the cloth so much. After sanding the whole thing smooth, I believe the surfboard guys then do one more coat of resin which is the one that will be polished to a shiny finish. (Our buddy Travis can probaby tell us that. :mrgreen: )
For what we are doing here, all we care about is that the surface is smooth. So instead of using resin, which would take another whole day to harden, I just filled the weave with bondo. A few coats of high build primer over that and we will be good to go.
One other thing I didn't mention is that for something like this where I want the surface to be fairly flat, I use sanding blocks as opposed to hand sanding. Here are a few of the ones I've made for different things - different sizes and grits for different purposes. (The chunk o' pipe works great for doing wing fillets on airplanes. :mrgreen: ) I am even using a block to wetsand the primer to keep everything flat. A final note about sanding blocks is that the sand paper will last much longer when glued to a block of wood. I guess because it is not flexing, so it doesn't break apart like it would if you were hand sanding. I've had some of these for years and they still work great!
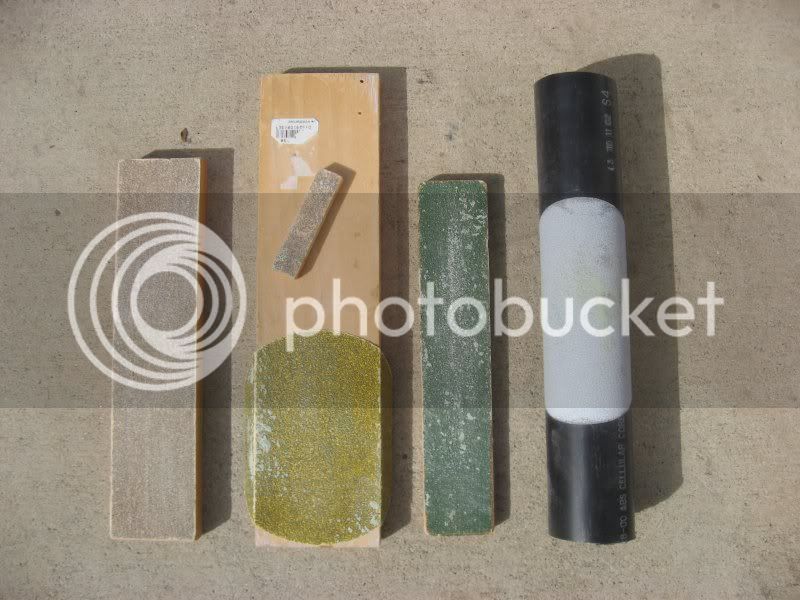
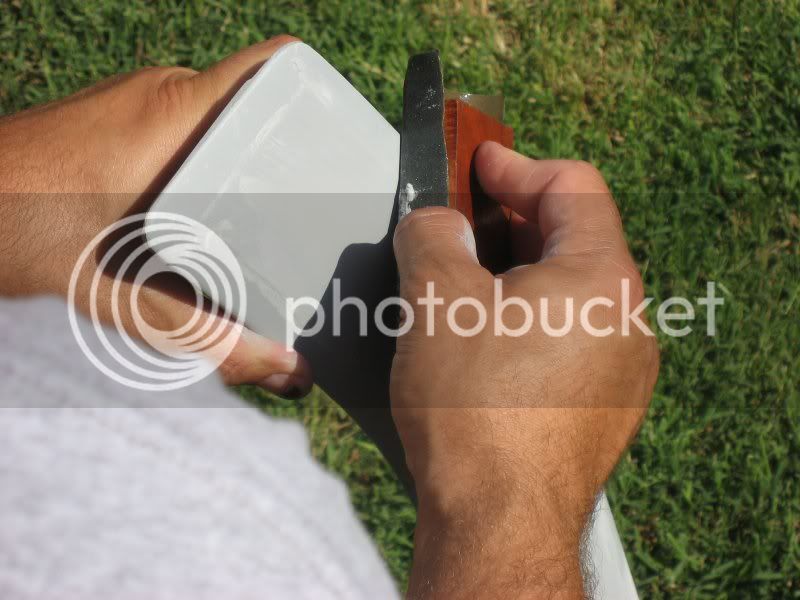